Top 14 Best Brewery Software in 2025
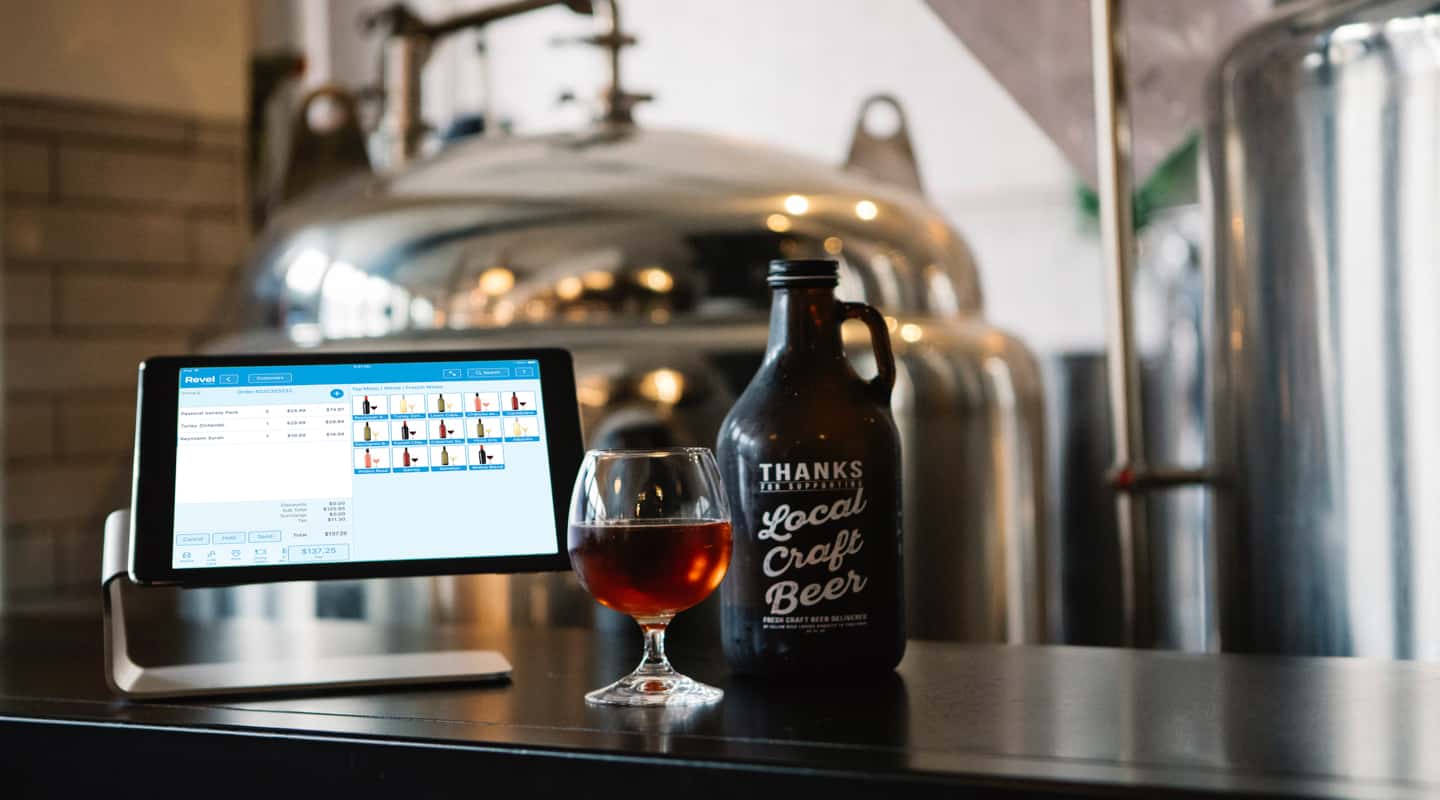
14 Best Brewery Software: In today’s fast-paced craft beer industry, you need robust digital solutions that work as hard as you do. Brewery software now governs everything from managing production schedules and tracking inventory to handling sales and ensuring regulatory compliance.
You face challenges like ingredient spoilage, production bottlenecks, and complex audit requirements as a dedicated brewer. Digital platforms are not just a luxury anymore; over 72% of breweries have deployed integrated systems to streamline operations, reduce errors, and drive efficiency.
Modern systems blend AI, IoT, and cloud technology, evolving from rudimentary recipe calculators into comprehensive ecosystems that cover every facet of your business.
This guide is designed specifically for you, whether you’re a small craft operation or managing a multi-location brewery. You will learn about the historical evolution of brewery software, understand its core benefits, and explore a detailed review of top industry solutions like Ekos, Ollie, VicinityBrew, and many more.
You will also gain insights into these technologies’ strategic implementation and future trends. By the end, you will be equipped with actionable recommendations and a clear roadmap for digitizing your operations. This article empowers you to make informed decisions that enhance compliance, reduce costs, and propel your business forward in an increasingly competitive market.
Understanding Brewery Software
Brewery software refers to specialized digital platforms that simplify and optimize the complex world of craft brewing. In recent years, these systems have transformed every part of your operations by automating workflows, minimizing errors, and providing valuable insights through real-time data. Let’s dive into these software solutions’ defining elements, historical context, and current market landscape.
Defining Brewery Management Systems
Brewery management systems are integrated digital tools that automate your brewing operations. They cover everything from recipe formulation and ingredient tracking to production scheduling, keg tracking, sales analytics, and regulatory compliance. Instead of laboriously updating manual spreadsheets, you now have automated dashboards that give you precise control over even the subtlest aspects of your process.
With features that include automated alerts, detailed KPI tracking, and real-time reporting, these systems improve efficiency dramatically. They focus on reducing manual errors, cutting operational costs, and helping you scale your business while maintaining high-quality standards. With brewery software on your side, you gain a powerful ally to navigate today’s rapidly evolving market.
Historical Context and Technological Evolution
The journey of brewery software mirrors the evolution of the craft beer industry itself. In the early days, brewers relied on manual record-keeping and basic recipe management software like BeerSmith, which emerged in the 1990s. As the industry grew, the need for more advanced solutions became apparent during the 2010s.
Early software provided basic recipe calculations but gradually expanded to incorporate ERP functionalities, data analytics, mobile accessibility, and IoT integration. Modern platforms like Ekos and Ollie now integrate seamlessly with production lines, manage raw ingredient inventories, and even offer RFID-based keg tracking.
The exponential growth in operational complexities drove these technological advancements, a reported 47% annual increase since 2020. This evolution has kept pace with industry demands and set new benchmarks for operational excellence.
Market Overview in 2025
The current market for brewery software is booming. In 2025, there will be over 10,000 breweries in the U.S. alone, with each business competing for its share of an industry that now owns nearly 25% of the total beverage market.
The global software market dedicated to brewing is projected to reach a staggering $1.2 billion, thanks to the increasing need for systems that offer automated TTB reporting, advanced keg tracking, and sustainability analytics.
With competition at an all-time high, embracing digitization is not optional; it’s a strategic imperative. You can leverage these cutting-edge tools to optimize production, ensure regulatory compliance, and increase profitability by reducing errors and minimizing waste.
Core Benefits of Digitization
Digitizing your brewery operations yields significant advantages. Error reduction is among the foremost benefits; manual discrepancies in inventory can drop from 18% to as low as 3% when automated tracking is implemented. Cost savings also play a pivotal role: mid-sized breweries report annual savings of around $85K due to improved waste management and production scheduling. Enhanced compliance is another critical benefit.
Automated excise and TTB reporting can reduce audit preparation time by as much as 70%, freeing you to concentrate on creative and strategic endeavors. In essence, by embracing brewery software, you streamline your operations and safeguard your business against regulatory pitfalls while boosting your bottom line.
Top 14 Best Brewery Software in 2025
In this section, you’ll find an in-depth comparison of the leading brewery software available in 2025. We have segmented the platforms into three categories: All-in-One Enterprise Platforms, Specialized Tools, and Solutions for Craft/Homebrewers. Each system is examined thoroughly via a consistent format, ensuring you understand how each tool can drive success in your brewing business.
All-in-One Enterprise Platforms: Enterprise platforms offer an integrated solution for managing production, inventory, sales, and compliance from a cohesive interface.
1. Ekos
Ekos is an all-in-one brewery management solution that integrates complex production, inventory, and sales processes into one seamless workflow. It’sIt’s intelligent dashboards and automated reporting capabilities empower you to monitor every detail of your brewing process.
In addition to TTB compliance modules, Ekos uses predictive analytics to help reduce waste and optimize raw material utilization. With a user-friendly interface and scalable features, it is ideal for mid-sized breweries that demand precise operational control and streamlined management procedures.
Key Features
- Over 150 automated production and sales reports
- RFID-based keg tracking to minimize losses
- Comprehensive TTB and regulatory compliance tools
- Customizable dashboards for real-time operational insights
- Seamless integration with POS, accounting, and ERP systems
Pros
- Intuitive interface with robust analytics
- Exceptional customer support and training resources
- Proven track record in reducing production waste and errors
Cons
- Higher subscription costs for smaller breweries
- Advanced features come with a learning curve.
- Occasional delays in software updates during high-demand periods
2. Ollie
Ollie offers a cloud-based brewery management platform with cutting-edge integration with third-party data tools, such as Next Glass, for market analytics. This solution is tailor-made to reduce manual errors and streamline compliance, especially for TTB audits.
Ollie’s tiered pricing model adapts to your business growth, making it accessible whether you’re starting or expanding your distribution network. Its mobile accessibility and real-time data tracking ensure you have complete insight into your production, inventory, and sales systems, making operational management efficient and flexible.
Key Features
- Cloud-based platform with multi-device access
- Seamless integration with third-party market analytics tools
- Automated TTB and other regulatory compliance features
- Tiered pricing models that accommodate different business sizes
- Real-time production scheduling and inventory management
Pros
- Easy integration with additional industry software
- Scalable to support growth in distribution and production
- Efficient handling of compliance and audit processes
Cons
- Additional plugins may be needed for full functionality.
- Beginners desire user interface improvements.
- Limited offline capabilities in areas with poor connectivity
3. VicinityBrew
VicinityBrew delivers a unique approach to brewery management by focusing on batch-level recipe customization and dynamic production adjustments. Its integration with IoT sensors enables real-time fermentation monitoring and precise control over ABV levels.
This system is perfect for experimental breweries that are continuously innovating while maintaining stringent quality standards. VicinityBrew’s detailed breakdown of production phases allows you to adjust workflows quickly, providing high production flexibility and ensuring every brew reaches its optimum quality. The platform is robust, versatile, and tailored for innovation and consistency.
Key Features
- Batch-level recipe customization with fine control
- Dynamic IoT sensor integration for real-time fermentation monitoring
- Tools for precise ABV tracking during production
- Detailed modules for production and cost tracking
- Integration capability with existing ERP systems
Pros
- Exceptional flexibility for experimental and traditional recipes
- Robust tracking tools for quality and production metrics
- Innovative integration of IoT technology for real-time monitoring
Cons
- High initial setup cost compared to other options
- Specialized hardware may be needed for full IoT functionality.
- Legacy system integrations may require extra configuration.
Specialized Tools: Specialized tools target specific aspects of brewery operations. These solutions enhance particular processes, such as keg tracking and fermentation analytics.
4. Kegshoe
Kegshoe is a specialized tool designed to mitigate keg loss through advanced RFID tracking technology. Its GPS-enabled system ensures you track every keg in real time, reducing losses significantly.
Kegshoe’s platform is ideal for brewers who maintain a large fleet of kegs and need precise control over logistics. With accurate tracking and loss analytics, Kegshoe provides actionable insights that enhance fleet management and reduce operational costs, ensuring you never lose sight of your valuable assets.
Key Features
- GPS-enabled RFID tracking for real-time keg location
- Automated alerts for expired or overdue kegs
- Integration with existing brewery management systems
- Detailed analytics on keg usage and loss
- Customizable notification and reporting tools
Pros
- Significantly reduces the risk of keg loss.
- Compatible with multiple brewery management platforms
- A user-friendly system that enhances overall fleet control
Cons
- Requires investment in RFID hardware
- Monthly subscription costs may be high for smaller breweries.
- Focused exclusively on keg tracking with limited additional features
5. Beer30
Beer30 leverages artificial intelligence to transform fermentation monitoring and production analytics. The system’s AI-driven algorithms monitor your brewing process, tracking temperature, humidity, and other critical metrics. It provides real-time alerts when batch discrepancies occur, reducing spoilage by up to 22%.
Beer30’s modular dashboard lets you customize key performance indicators for each production phase. Ideal for small and medium-sized breweries, this solution offers actionable insights that help maintain product quality and consistency with minimal manual intervention.
Key Features
- AI-enhanced fermentation monitoring and quality control
- Customizable, modular dashboard for KPI tracking
- Automated alerts for detecting batch discrepancies
- Integration with temperature and humidity sensors
- Detailed historical data and trend analysis reports
Pros
- Substantially reduces spoilage and batch errors.
- Offers real-time, actionable insights in production
- User-friendly interface with customizable features
Cons
- Sensor calibration may be required periodically.
- High dependence on stable internet connectivity
- Some advanced features require professional technical support.
6. Breww
Breww prioritizes mobility and accessibility with a mobile-first design that ensures you stay connected even on the go. Its offline functionality empowers you to manage your production and inventory without relying on continuous internet access.
Breww is built for the modern brewer who often works in remote or challenging environments, ensuring your operations remain uninterrupted. With real-time updates and an intuitive interface, Breww provides comprehensive oversight of your brewing operations, making tracking every detail from raw material sourcing to finished product distribution efficient and straightforward.
Key Features
- Mobile-first design with robust offline capabilities
- Real-time tracking for production and inventory management
- User-friendly interface optimized for smartphones and tablets
- Seamless synchronization once connectivity is restored.
- Customizable alerts and notifications for operational updates
Pros
- Enhances on-the-go management of brewery operations
- Reduces downtime during connectivity issues
- Ideal for multi-location mobile teams
Cons
- Lacks some advanced desktop reporting features
- It may require additional configuration for legacy system integration.
- Occasional syncing delays noted in remote regions
Solutions for Craft/Homebrewers: These platforms are tailored to meet the specific needs of craft and homebrewers, focusing on recipe management and streamlined production tracking.
7. Brewfather
Brewfather is the favored cloud-based solution among homebrewers and small craft operations. It focuses on simplifying recipe formulation, batch tracking, and ingredients management. With integrated tilt hydrometer support and a vibrant community of over 500,000 users, Brewfather transforms brewing into a collaborative experience.
Although it emphasizes ease of use and community engagement, it also provides essential production tracking tools that help you iterate and perfect your recipes. This platform is perfect for keeping your brewing process straightforward while performing in-depth operational analysis.
Key Features
- Cloud-based recipe and batch management
- Compatibility with tilt hydrometers and smart devices
- Automated brewing calculations and conversion tools
- Active community for sharing and refining recipes
- Detailed production logs and tracking for quality control
Pros
- Intuitive design tailored for home and small-scale brewers
- Strong community support and recipe-sharing tools
- Rapid setup and minimal training requirements
Cons
- Limited tools for regulatory compliance in larger setups
- Fewer integration options with enterprise-level systems
- Reporting features are basic compared to full-scale ERP solutions.
8. ViewPlan BMS
ViewPlan BMS is a comprehensive brewery management tool for nano to mid-sized operations. Its unique one-time payment model helps you save on recurring subscription costs, making it a cost-effective choice. ViewPlan covers the entire brewery operations by providing end-to-end management, from raw material tracking and production scheduling to inventory control and compliance.
Its intuitive interface minimizes the learning curve, allowing you to deploy the solution quickly and efficiently. ViewPlan BMS is highly adaptable, ensuring you can scale your system as your production demands evolve.
Key Features
- One-time payment model for predictable long-term expenses
- End-to-end production, inventory, and compliance management
- Customizable dashboards designed to highlight critical data
- Powerful scheduling tools to optimize batch production
- Seamless integration with accounting, POS, and ERP systems
Pros
- Predictable, cost-effective pricing structure
- Comprehensive management across all brewery functions
- Minimal training is required, thanks to an intuitive interface.
Cons
- Limited remote accessibility due to less cloud integration
- Some modern mobile features are not fully refined.
- Advanced analytics may require third-party add-ons.
Additional Notable Brewery Software Solutions: Based on your operational needs, several other standout systems might be worth considering in addition to our primary reviews.
9. BrewMan
BrewMan brings versatility to brewery management by consolidating production schedules, ingredient tracking, and compliance reporting into a robust tool. Its all-encompassing dashboard provides clear insights into operations, helping you monitor every production phase efficiently.
Designed with both traditional and modern craft breweries in mind, BrewMan facilitates a smooth operational flow without overcomplicating the process. Whether scaling production or optimizing a minor craft operation, BrewMan’s adaptable interface and data-driven analytics ensure you maintain control over quality and timing across all processes.
Key Features
- Unified dashboard for production, sales, and inventory management
- Automated compliance and audit reporting functions
- Customizable analytics and real-time reporting
- Integration capabilities with various logistics, accounting, and ERP systems
- Real-time ingredient tracking and batch monitoring
Pros
- Consolidates multiple processes into one streamlined solution
- User-friendly design minimizes training time.
- Adaptable modules that cater to different brewery sizes
Cons
- Lacks deep integration with advanced IoT technology
- Setup for complete ERP integration can be complex.
- Customer support response times may vary during high-volume periods.
10. ShipCompliant
ShipCompliant is tailored to manage the industry’s rigorous regulatory requirements for alcohol. It automates TTB and state excise reporting while streamlining shipping logistics and compliance documentation. Suppose you struggle with managing detailed audit trails or shipping paperwork.
In that case, ShipCompliant provides an all-in-one platform to handle these tasks efficiently. With its automated workflows, the system reduces the administrative burden during audits, ensuring you remain compliant with minimal manual intervention.
Key Features
- Automated TTB and state-level excise compliance reporting
- Integrated shipping and logistics solution
- Step-by-step audit preparation and compliance checklists
- Real-time regulatory updates and alerts
- Customizable reporting for compliance documentation
Pros
- Drastically simplifies complex regulatory compliance tasks.
- Reduces manual errors in shipping and documentation
- Provides ongoing updates to meet changing regulatory standards
Cons
- Steeper learning curve for beginners unfamiliar with regulatory software
- Premium pricing may deter smaller operations.
- Limited integration with non-compliance-focused systems
11. Ohanafy
Ohanafy is a cloud-based brewery management solution that unifies production, inventory, and distribution tracking under one portal. Its clean and simple design lets you manage your operations with minimal hassle, making it ideal for breweries striving for efficiency and scalability.
With regular feature updates and a focus on remote accessibility, Ohanafy ensures consistent performance, whether in the brewery or on the go. Its emphasis on ease of use makes it an excellent choice for those transitioning to digital management platforms for the first time.
Key Features
- Cloud-based system for seamless remote management
- Unified modules covering production, inventory, and distribution
- Real-time automated updates and reporting
- Scalable design to support future growth
- Customizable workflows for tailored operational management
Pros
- Simplifies remote monitoring and management significantly
- A User-friendly interface minimizes disruption during the transition.
- Regular updates introduce innovative features consistently.
Cons
- Mobile application features could be more advanced.
- Some integrations may require additional customization.
- Occasional syncing delays reported by users during heavy load periods
12. Brewoptix Craft Software
Brewoptix Craft Software caters to the precise needs of craft breweries by centralizing recipe management, inventory control, and quality analysis. Its analytical dashboards provide deep insights into every step of production.
With customizable modules that adjust to various brewing scales, Brewoptix offers a blend of precision and flexibility. Designed for craft brewers who demand meticulous control and real-time adjustments, this solution helps you maintain high quality and consistency across every batch, from experimental brews to large-scale production.
Key Features
- Centralized management of recipes, inventory, and production
- Detailed analytical dashboards and reporting tools
- User-friendly interface enabling rapid recipe adjustments
- Customizable modules for diverse production scales
- Integration with quality control and compliance systems
Pros
- Adapts to both detailed artisanal and large-scale production needs
- Provides deep, actionable data insights
- Minimizes training time with its intuitive design
Cons
- Premium pricing may be a barrier for ultra-small breweries.
- The advanced configuration needed for a full analytics suite
- External tool integrations may have some limitations.
13. Crafted ERP
Crafted ERP is an enterprise-level solution that merges industry-specific functionalities with full ERP capabilities. It gives you an absolute view of every stage of your brewery, from ingredient sourcing through production to sales and financial management.
With its robust integration capabilities and scalable design, Crafted ERP suits breweries in high-growth phases. It offers extensive customization options that allow you to mold the system to your business’s unique needs while streamlining data flow and ensuring regulatory compliance.
Key Features
- Comprehensive ERP integration spanning production, inventory, and finance
- Real-time financial reporting and inventory controls
- Scalable modules tailored to growing brewery operations
- Customizable dashboards for performance monitoring
- Seamless integration with third-party vendor systems
Pros
- Offers an enterprise-level solution for complete operational oversight
- Highly scalable, adapting as your business evolves
- Extensive customization to suit unique operational workflows
Cons
- Implementation can be complex and time-consuming.
- A steeper pricing model is not suitable for tiny breweries.
- Ongoing technical support is necessary for complete system integration.
14. Meez
Meez adopts a modern cloud-based approach to streamlining daily brewery operations through automation and comprehensive connectivity. It aggregates production, inventory, and sales data to provide clear, actionable insights.
With its sleek interface and real-time reporting, Meez helps you optimize waste reduction, manage compliance, and drive profitability. Its design ensures you spend less time wrestling with data and more time focusing on perfecting your craft. This solution is perfect if you’re looking for operational agility and a straightforward digital management system.
Key Features
- Cloud-based platform with centralized data management
- Automated tracking for production, inventory, and sales metrics
- Real-time analytics and reporting dashboards
- Customizable widgets for tailored user experiences
- Seamless integrations with popular industry tools
Pros
- Improves operational efficiency through automation
- Straightforward design minimizes the learning curve.
- Real-time data streamlines decision-making processes.
Cons
- It may not offer as many advanced customization options as enterprise systems.
- Fewer integrations with some older legacy software
- Occasional performance lags during peak operational hours.
Operational Efficiency and Core Features of Modern Brewery Software
Operational efficiency is the backbone of a successful brewery. Modern brewery software solutions are designed to address your pain points head-on. Let’s explore these systems’ critical benefits and core features, ensuring you can focus on brewing the perfect craft beer.
- Inventory Management:
- Your inventory is the lifeblood of production, and modern software drastically improves how you manage it. Automated raw material alerts reduce stockout rates by 12%, while real-time expiry tracking lowers waste levels by up to 19%.
- With integrated barcode scanning and RFID capabilities, you no longer need to worry about discrepancies or manual counting errors. You obtain a seamless flow of information that improves ordering precision and minimizes human error.
- Production Modules:
- Accurate production planning ensures batch consistency. Modern brewery software provides batch-level tracking, maintaining an ABV variance of less than 0.5%.
- IoT sensors integrated into fermentation tanks reduce manual monitoring labor by up to 8 hours per week. With detailed production metrics and real-time alerts, you can fine-tune your production processes and quickly address any discrepancies before they impact quality.
- Financial Tools:
- Your bottom line matters. Automated cost-of-goods-sold (COGS) calculations and financial reporting modules improve margin accuracy by over 27%.
- With an integrated approach, you can track expenses, optimize labor costs, and monitor profitability. This data-driven approach boosts operational efficiency and provides actionable insights that drive sustainable growth.
- Mobile Capabilities:
- Modern software solutions have mobile functionalities that empower you to manage operations anywhere.
- With mobile access and barcode scanning integration, inventory count errors dropped by 92%. These features allow immediate oversight, whether on the production floor or the go, ensuring your business stays agile and responsive.
Implementation Strategies for Success
Adopting a brewery management system can be transformational, but a structured implementation strategy is key to your success. Here’sHere’s how you can ensure a smooth transition:
Needs Assessment Checklist
Before diving into implementation, assess your current operations:
- Production Volume: Compare ≤1k bbl versus 10k+ bbl operations.
- Compliance Requirements: Identify your needs for TTB, state excise, and sustainability reporting.
- Distribution Model: Determine if you manage logistics internally or depend on third-party logistics.
- Budget and ROI: Evaluate costs that range from $35 to $500 per month and factor in the break-even period.
A typical payback occurs within 14 months through savings in waste reduction and improved order fulfillment.
Phased Rollout Strategy
Implement your software in phases:
- Inventory Management: Start with automated tracking to reduce errors immediately.
- Production Modules: Roll out batch management tools to standardize recipes.
- Sales & Compliance: Integrate the compliance modules to streamline TTB and audit preparation
The phased implementation ensures that each module is fully adopted and the learning curve is manageable, reducing potential disruptions in operations.
Training and Support
Invest in role-specific training sessions:
- Operational Training: For production managers and inventory supervisors.
- Technical Training: For IT support and system administrators.
- Vendor Support: Ensure you have access to dedicated support teams to address issues promptly. Studies have shown that this can cut transition time by 30%.
Hidden Savings
Look beyond the initial cost:
- Order Fulfillment: Automated procedures can improve fulfillment speed by up to 30%, reducing labor costs.
- Predictive Analytics: Utilizing data can help avoid surplus production, cutting waste by approximately 40%.
- Addressing these elements, you achieve a smoother transition while safeguarding your operations against common pitfalls.
Future Trends in Brewery Technology
Staying ahead means tapping into what’s on the horizon. Here are the future trends poised to shape brewery software in the coming years:
- Artificial Intelligence and Machine Learning:
- AI integration in recipe optimization programs can yield up to 15% savings on ingredient costs. AI algorithms can predict production bottlenecks and suggest the most cost-effective tweaks to your processes, ensuring your brewery remains efficient and profitable.
- IoT-Driven Process Automation:
- IoT sensors are set to revolutionize fermentation monitoring. Real-time tank sensors continuously track temperature, pH, and humidity levels, reducing spoilage by an extra 14% while minimizing manual labor during critical production stages.
- Blockchain for Traceability:
- Imagine having a 100% transparent batch-to-source verification system. Blockchain technology is being tested to ensure each ingredient’s origin is authenticated, building consumer trust and ensuring regulatory compliance with traceability.
- Sustainability Analytics:
- Environmental and social governance (ESG) remains at the forefront. Integrated water and energy dashboards help brewers monitor and reduce environmental impact. These analytics accelerate certification processes by up to 22%, ensuring your operations perform economically and align with sustainability goals.
- Custom IoT Integrations:
- Future platforms will focus on customizable IoT modules that brew technology tailored to your production layout. These integrations offer increased precision in predictive maintenance and quality control, ensuring fewer production bottlenecks and improved output consistency.
Conclusion
As you explore digital solutions for your brewery, it’s clear that modern brewery software systems are not just technological luxuries; they are strategic business enablers. Embracing these solutions means you’re reducing errors and operational costs and unlocking a data-driven approach that propels your production quality and regulatory compliance to new heights.
The right system, whether an all-in-one enterprise solution like Ekos or a specialized tool like Kegshoe, can enhance your ability to track, monitor, and optimize every brewing process step. Remember to prioritize systems that scale with your business, offer real-time insights, and integrate seamlessly with your existing workflows. Hands-on trials with at least three different platforms and in-depth assessments of API capabilities and vendor support can ensure you select the perfect platform tailored to your unique needs.
In 2025’s competitive market, staying ahead requires you to leverage technology that simplifies daily operations and drives long-term growth. With the rising complexity of production and compliance requirements, you must harness the power of these systems to remain agile, efficient, and customer-focused.
We recommend engaging with vendors, taking advantage of free demos, and investing in comprehensive training programs to maximize ROI. Adopting robust brewery software can reduce waste, mitigate risks, and drive innovation in your product offerings, ensuring your brewery is ready for future challenges and opportunities.
If you found this guide valuable, don’t hesitate to subscribe to our newsletter for more insights, leave a comment below sharing your experience, and share this article with fellow brewers. Empower your operations by embracing technology that transforms your passion into precision and exceptional quality.
Frequently Asked Questions
What is brewing software?
Brewing software refers to digital solutions designed to manage the beer production process. These platforms integrate recipe formulation, inventory management, production scheduling, quality control, and regulatory reporting into one cohesive system.
By automating routine processes, brewery software reduces human errors and maximizes efficiency. This innovative technology enables brewers to obtain real-time insights, ensuring consistency and streamlined operations from small craft setups to large commercial breweries.
What are the benefits of using brewery software?
Brewery software offers significant benefits by streamlining your operational workflows. It automates tasks like production scheduling, inventory tracking, and compliance reporting, which minimizes manual errors and reduces operational costs.
You can quickly monitor performance and make informed decisions with real-time data analytics and reporting. Enhanced scheduling and quality control translates into reduced waste and improved product consistency, making brewery software an indispensable tool for maintaining high standards and boosting profitability in today’s competitive craft beer industry.
How does the best brewing software improve production efficiency?
The best brewing software enhances production efficiency through automation and data integration. It provides real-time monitoring of batch production, consolidates inventory updates, and tracks quality control metrics.
The system minimizes errors and swiftly identifies production bottlenecks by reducing manual intervention. You can adjust processes with detailed analytics and predictive alerts, ensuring continuous improvement.
This streamlined operation maintains consistent beer quality and allows you to focus on innovation and expand your market presence.
What features should I expect from top brewery software?
Top brewery software typically offers a comprehensive suite of features, including recipe management, inventory control, production scheduling, and automated compliance reporting.
Many systems integrate with IoT sensors for real-time monitoring, providing fermentation and temperature control alerts. Additional benefits include sales analytics, mobile access capabilities, and customizable dashboards.
These features empower you to oversee every aspect of production and streamline operations, ensuring your brewery maintains high-quality standards while effectively managing resources and meeting regulatory requirements.
How does brewery software help with regulatory compliance?
Brewery software plays a pivotal role in regulatory compliance by automating critical reporting functions. It consolidates and organizes production data for TTB filings, state excise reports, and other regulatory documents.
Compliance becomes less cumbersome and more accurate with real-time record-keeping and audit trails. This automation minimizes human error and reduces administrative workload.
By safeguarding your operations through timely, reliable reporting, brewery software ensures that your facility consistently meets industry regulations and avoids costly penalties associated with non-compliance.
Is brewery software suitable for both small and large breweries?
Yes, brewery software is designed to be scalable and adaptable, making it suitable for small craft operations and large commercial breweries. Many systems offer modular features and tiered pricing plans that allow you to choose the functionalities that match your current needs.
Whether you require basic production tracking or a full-scale ERP integration for extensive operations, brewery software can adjust to your requirements. This flexibility ensures that the software evolves with you as your business grows, maintaining consistency and efficiency across all production stages.
How does brewery software enhance inventory management?
Brewery software significantly improves inventory management by automating tracking raw materials and finished products. Integrated barcode scanning and RFID technology ensure that inventory levels remain accurate and up to date, reducing the risk of overstocking or stockouts.
The system provides real-time updates and notifications when materials are low, enabling prompt reordering. This automation not only minimizes waste but also supports efficient budgeting and planning.
With clear visibility over inventory, you can optimize resource allocation and sustain smooth production cycles throughout your brewery.
Can brewery software help reduce operational costs and waste?
Absolutely, brewery software is a powerful tool for reducing operational costs and minimizing waste. Automating critical tasks such as production scheduling, quality control, and inventory management significantly lowers the potential for human error and resource mismanagement.
With detailed, real-time analytics, you can identify inefficiencies and adjust production processes. These improvements lead to more efficient resource utilization, reduced waste, and substantial cost savings over time, ensuring that your brewery operations remain economically and environmentally sustainable.
How do I choose the best brewing software for my brewery?
Choosing the best brewing software involves evaluating your brewery’s unique requirements, production scale, and growth potential. Look for solutions offering features that match your needs, such as inventory tracking, compliance reporting, real-time analytics, and mobile access.
Consider integration capabilities with your existing systems and the software’s scalability. Trial periods, peer reviews, and vendor support quality are critical factors. By comprehensively assessing these elements, you can select a brewery software solution that enhances operational efficiency, reduces waste, and provides long-term value to your business.
What trends are shaping the future of brewery software?
Advancements like artificial intelligence, IoT integration, blockchain traceability, and enhanced cloud-based functionalities are shaping the future of brewery software. These trends enable more precise production forecasting, real-time sensor monitoring, and secure supply chain tracking.
Modern systems increasingly incorporate intelligent analytics to optimize ingredient usage and improve quality control. As brewery software evolves, expect even more automated, data-driven solutions that empower brewers to innovate, increase efficiency, reduce costs, and meet industry standards in a rapidly changing market.